October 17, 2024
The Human Factor in Modern Supply Chain Management
These days, automation, artificial intelligence (AI), and robotics play a prominent role in enhancing efficiency and reducing costs. However, despite the advancements, human logistics remains critical for successfully executing supply chain operations.
While machinery and technology can perform repetitive tasks with precision, it is human intuition, decision-making, and problem-solving abilities that ensure supply chains are flexible and adaptable to unforeseen challenges. Let’s explore the role of people in logistics and the importance of human factors in modern supply chain management.
Focus on the Team, Not the Assets
Non-asset-based carriers are intermediaries between clients and transportation services, connecting companies with third-party carriers, warehouses, and logistics providers. They do not own trucks, warehouses, or shipping facilities but rely on their extensive network of partners to offer a range of logistics services. This business model emphasizes flexibility, cost-effectiveness, and the ability to scale quickly.
Nevertheless, what differentiates these carriers is their ability to integrate human factors into their operations. From managing vendor relationships to going through complex reverse logistics processes, human judgment is critical for ensuring the seamless coordination of services.
Human Factors in Last-Mile Logistics
The final leg of the delivery process is often considered the most challenging and expensive part of the supply chain. It involves delivering goods from a transportation hub to their final destination, and this stage is filled with potential issues such as delays, incorrect deliveries, or damaged goods.
Here, human logistics are crucial. Drivers, customer service representatives, and logistics coordinators must exercise adaptability and real-time decision-making. While GPS systems and route optimization software are helpful, only humans can manage unexpected traffic, weather disruptions, or customer-specific requests. Their ability to assess on-the-ground conditions and adjust accordingly is key to ensuring timely, accurate deliveries.
Moreover, last-mile logistics involves significant customer interaction. The human factor is crucial in handling customer concerns, managing expectations, and resolving any last-minute issues. This individualized touch can turn a potentially harmful customer experience into a positive one, ensuring customer satisfaction and loyalty.
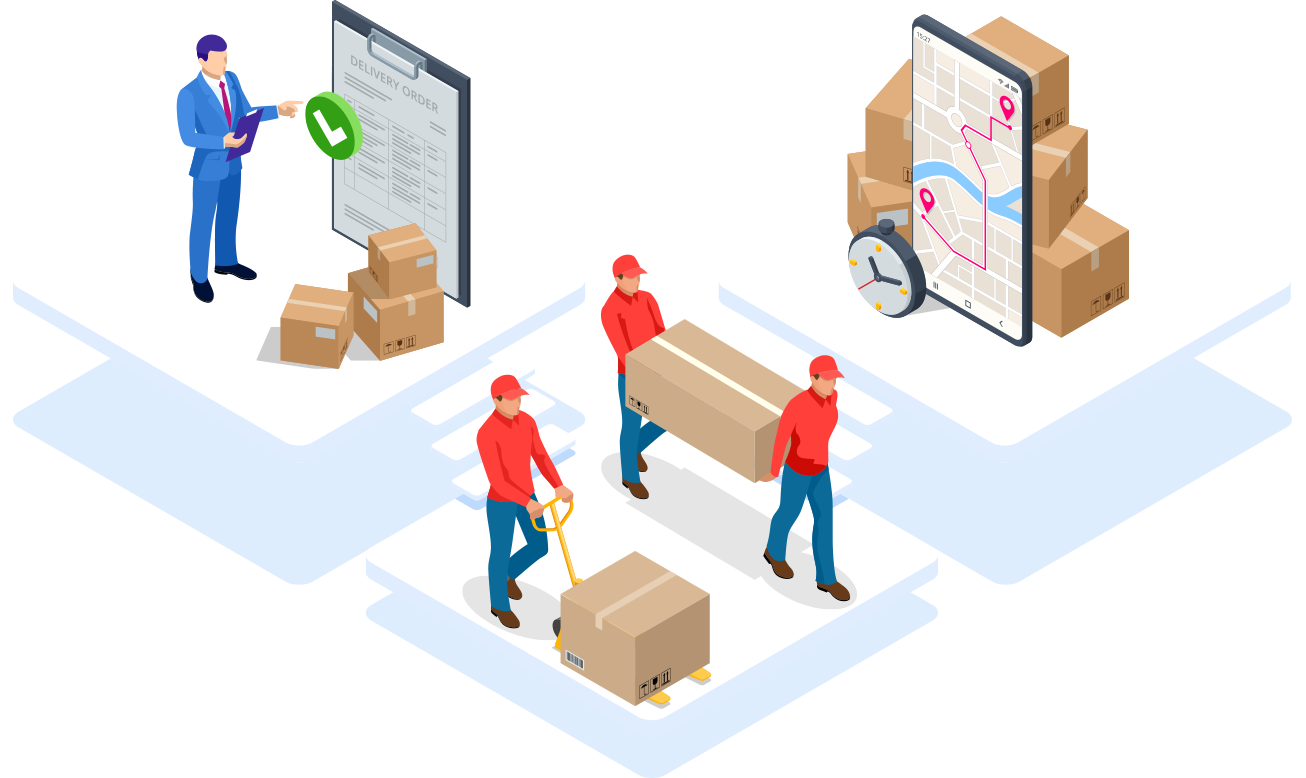
Strategic and Human Warehousing
Strategic warehousing is essential for ensuring inventory is stored and distributed efficiently, allowing businesses to meet customer demand without incurring excess costs. While automation has revolutionized many warehousing processes, like inventory tracking and order picking, human warehousing remains vital for overseeing complex operations and ensuring accuracy in more nuanced tasks.
Warehouse managers and staff must continuously monitor supply levels, manage personnel, and adjust operations to account for fluctuations in demand. The human factor comes into play in situations that require problem-solving and quick decision-making, such as handling inventory discrepancies or unexpected supply chain disruptions. Human oversight is also essential for maintaining safety protocols, quality control, and regulatory compliance.
The ability to multitask and manage diverse teams is crucial, particularly for non-asset-based carriers who must coordinate between multiple partners and warehouse facilities. The knowledge and experience of warehouse personnel can make all the difference in ensuring that goods move smoothly through the entire supply chain.
Where Human Expertise Shines
Expedited shipping is often used when companies need to meet tight deadlines or when time-sensitive goods must be delivered quickly. While automation can optimize route planning and shipment scheduling, the people factor is essential for managing unexpected situations, such as weather delays, mechanical breakdowns, or customs issues.
Human logistics coordinators are the backbone of expedited shipping services, ensuring that each shipment meets its delivery window without compromising quality. They can think critically, communicate effectively with stakeholders, and make rapid decisions, becoming an invaluable asset to maintaining the integrity of the supply chain.
Similarly, white glove services and premium delivery options that often include setup or installation depend heavily on the human factor. Customers expect high professionalism, attention to detail, and personalized service. Employees involved in white glove services must have technical expertise and excellent communication and customer service skills. These human factors are crucial for ensuring a seamless, stress-free experience for the end customer.
Building Relationships and Trust
Vendor management is another area where the human factor significantly impacts supply chain success. Vendor management involves coordinating with multiple suppliers, carriers, and third-party logistics providers for non-asset-based carriers to meet customer demands. Human factors in management, such as building solid relationships and trust, are essential for creating a reliable and responsive supply chain network.
Negotiating contracts, resolving disputes, and maintaining open lines of communication are factors that determine the quality of partnerships within the supply chain. Human intuition and emotional intelligence play a role in these relationships, ensuring that all parties work harmoniously to meet mutual goals.
Vendor management also requires a deep understanding of the factors affecting the supply chain. Logistics managers must anticipate potential issues, such as supplier shortages or transportation delays, and proactively develop contingency plans to mitigate these risks. Human oversight ensures that problems are addressed quickly and efficiently, minimizing disruptions.
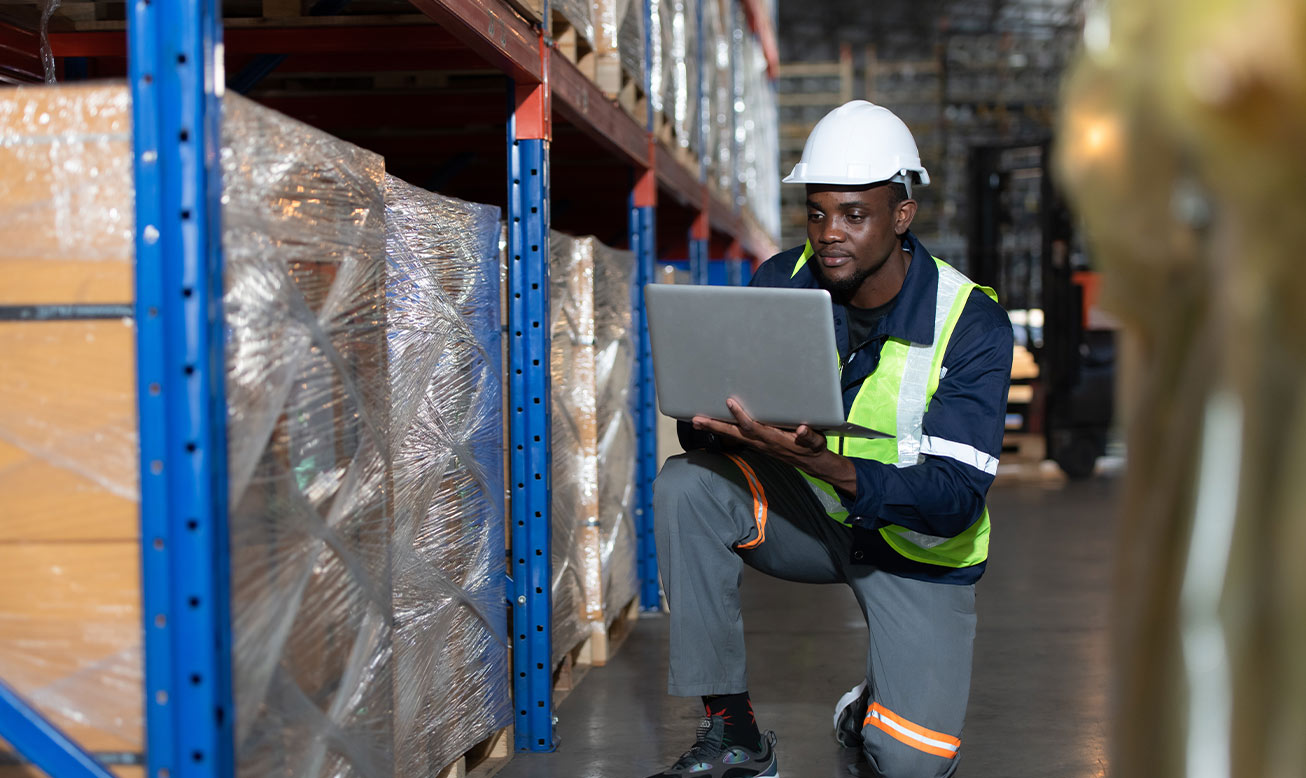
A Human-Centric Process
Reverse logistics is the process of returning items, whether from retailer to manufacturer or distribution center. It is an often overlooked operation but is a critical component of supply chain management. Unlike forward logistics, which focuses on getting products to specific locations, reverse logistics is fraught with uncertainty. Goods may be returned for various reasons, including defects, customer dissatisfaction, or end-of-life recycling.
Here, human factors in production and logistics management play a vital role in assessing and processing returns. Employees must determine whether products are suitable for resale, repair, or recycling, often requiring careful inspection and judgment. Furthermore, reverse logistics involves significant customer interaction, where empathy and problem-solving skills are crucial for handling complaints and ensuring a smooth return process.
The Ongoing Importance of the Human Factor in Supply Chain Management
Despite the rise of automation and technological advancements, human logistics remains the backbone of modern supply chain management. Non-asset-based carriers rely heavily on human intuition, expertise, and decision-making. By prioritizing the people factors in their operations, non-asset-based carriers can offer flexible, responsive, and customer-focused logistics solutions that keep businesses running efficiently.
At Last Mile Logistics, we deeply value the hard work of our staff and those of our extended network of partners. Whether managing vendors, optimizing warehouse operations, or ensuring customer satisfaction, our human insight and adaptability will be critical to the success of your supply chain operations. So please call Arnie today so we can evaluate your transportation needs.