September 5, 2024
Lessons Learned from Recent Supply Chain Disruptions
Recent world crises—climate, pandemics, and geopolitical issues—have provoked fundamental changes in commerce, particularly in supply chain management. Despite the global potential to affect the locals, many non-asset-based carriers—companies that do not own the physical logistics assets but coordinate and manage transportation services—have shown extraordinary resilience during recent stormy times. These companies have survived and thrived by adopting innovative strategies and learning from recent disruptions. Let’s discuss the critical disruptions that recently came to pass and how logistics players have learned their fair share of supply chain management lessons.
Enhancing Supply Chain Flexibility
One of the most valuable lessons from recent disruptions in the supply chain is the importance of flexibility. Traditional supply chains, which were often rigid and reliant on specific routes or suppliers, struggled to adapt to sudden changes. Non-asset-based carriers, however, had the advantage of flexibility built into their operations. By not being bound to specific assets, these third-party logistics providers could redirect fast, adjust routes, find alternative suppliers, or even change modes of transportation as needed.
Flexibility in supply chain management is all about the ability to quickly respond to demand fluctuations, supply shortages, or logistical bottlenecks. Companies with supply chain management issues often find themselves stuck in rigid frameworks, unable to respond to a more fluid situation. By contrast, those businesses that prioritized flexibility could go on and even gain a competitive edge.
For managers looking to enhance their supply chain flexibility, it is crucial to invest in dynamic planning tools, maintain diverse supplier networks, and develop strong relationships with logistics partners that provide a vast option of adaptable solutions. The lesson here is clear: flexibility and agility are key to overcoming supply chain challenges in an unpredictable world.
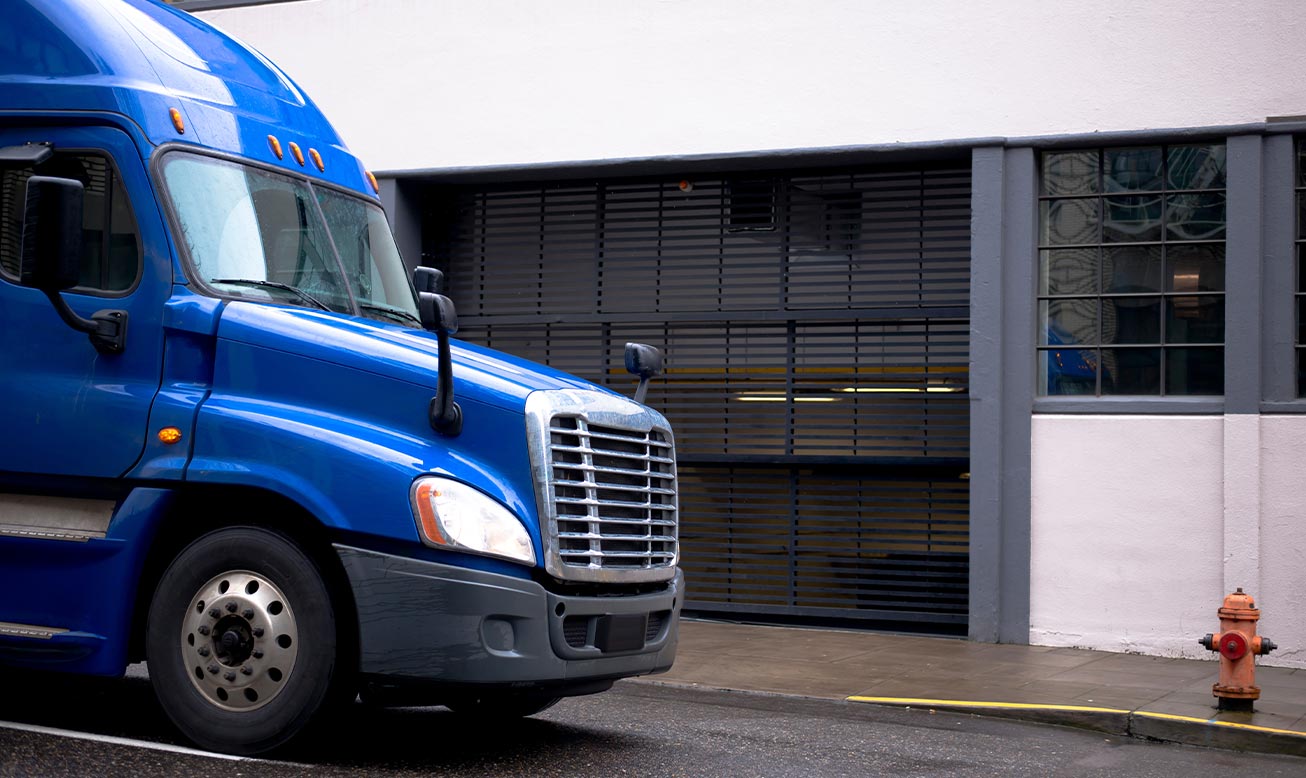
Accounting for External Influences
Another meaningful lesson learned is the need to factor external influences into supply chain processes. For example, the pandemic showed us how external factors, such as government regulations, border closures, and shifts in consumer behavior, can drastically impact supply chains. Companies with messy supply chains often fail to consider these external variables, resulting in significant disruptions.
Non-asset-based carriers have considerable experience in closely monitoring external influences and incorporating them into their planning processes to better anticipate and mitigate risks. This approach involves staying informed about geopolitical events, economic trends, and environmental factors that could affect supply chains. For instance, how a sudden surge in e-commerce could strain delivery networks or how a new trade regulation might disrupt cross-border logistics.
Incorporating external factors into supply chain management involves more than just awareness; it requires proactive adjustments to logistics strategies. Companies should be ready to adapt their operations based on an evolving industry, whether that means shifting to local suppliers, adjusting inventory levels, or re-routing shipments. By doing so, they can avoid the pitfalls faced by businesses with supply chain management issues and emerge stronger when facing uncertainties.
Proactive Risk Management
Risk management has always been a cornerstone of supply chain management, but the recent disruptions have unveiled the ongoing need for a more foresighted approach. Many companies discovered that their risk management strategies were reactive rather than proactive, leaving them vulnerable when disruptions occurred. In contrast, non-asset-based carriers that took a step forward were better positioned to manage supply chain disruptions.
Proactive risk management involves identifying potential threats before they appear and developing contingency plans to address them. These processes often include diversifying suppliers, investing in technology that offers better visibility across the supply chain, or creating strategic reserves of critical inventory. Companies with supply chain management issues often forget to plan ahead, resulting in significant challenges when disruptions occur.
One of the logistics lessons learned from recent events is the importance of continuous risk assessment and scenario planning. By performing regular reviews and updates of their risk management strategies, companies can stay ahead of potential disruptions and ensure that they are prepared to respond effectively. The aim should not be to survive disruptions but to thrive by turning challenges into opportunities for growth and innovation.
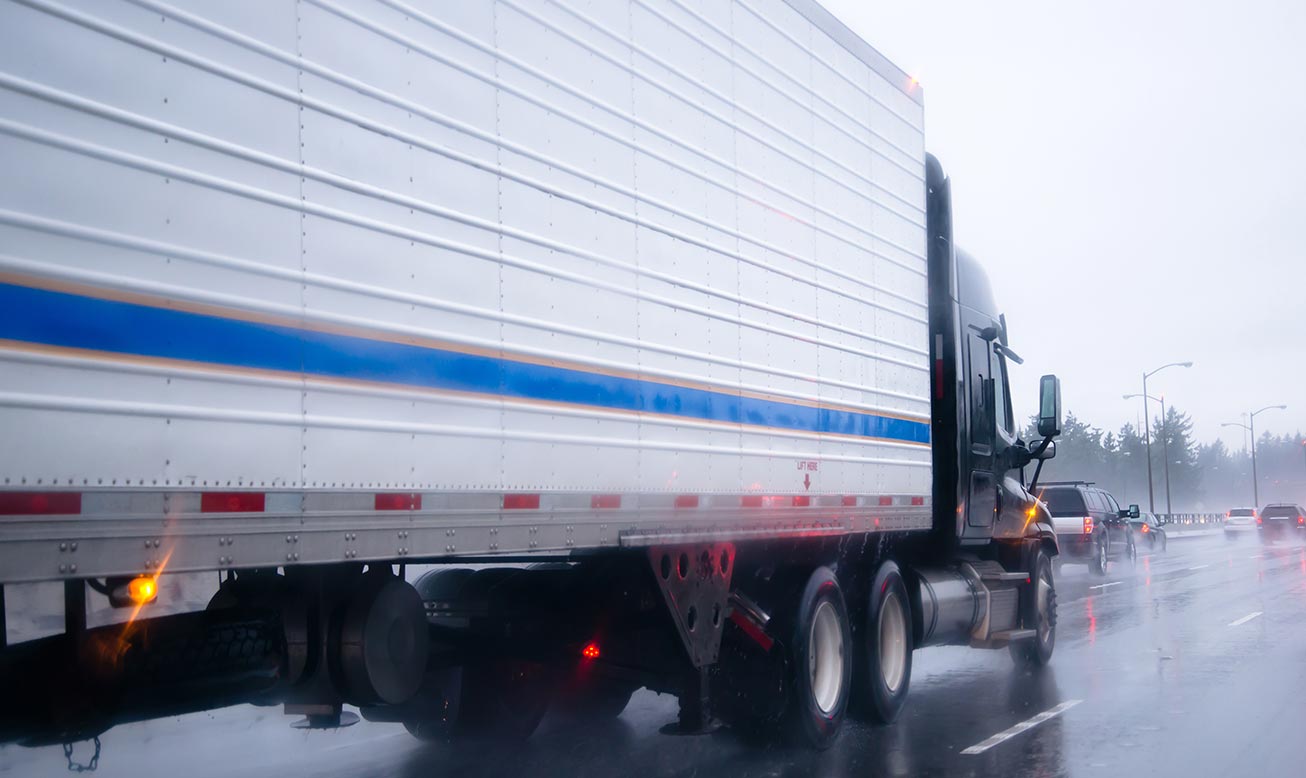
Strengthening Cybersecurity
As supply chains become increasingly digitized, the need for robust cybersecurity measures has never been greater. The time we spend working remotely has accelerated the spread of digital technologies in supply chain management, but it has exposed some vulnerabilities that cyber threats can exploit. Companies with supply chain problems often overlook the importance of cybersecurity, leading to breaches that exacerbate their challenges.
3PLs, which rely heavily on digital platforms for coordination and communication, have acknowledged the critical matter of enforcing cybersecurity standards in the workplace. Strategies for this approach include:
- Implementing strong encryption protocols
- Conducting regular security audits
- Ensuring that all stakeholders are skilled in best practices for cybersecurity
The lesson here is that dealing with supply chain disruptions in the digital age requires more than just physical logistics; it requires a secure digital infrastructure that can resist cyber threats. Companies that neglect cybersecurity risk are more prone to face financial losses and, most importantly, damage to their reputation and customer trust in the long term. By investing in robust cybersecurity measures, companies can protect their processes and ensure that their operations remain resilient in the face of both physical and digital disruptions.
Investing in Compliance Technology
Making peace with regulations is a critical factor in supply chain management, especially in an environment where rules and laws constantly evolve. In recent years, many regulatory challenges, from health and safety standards to trade restrictions, have added complexity to supply chain operations. Companies with supply chain management issues often struggle to keep up with these changes, leading to disruptions and compliance breaches.
Non-asset-based carriers have proved that investing in compliance technology is essential for keeping up with a complex regulated industry. Compliance technology can help businesses monitor and adhere to regulations in real-time, reducing the risk of non-compliance and associated penalties. This technology can also streamline reporting processes, ensuring that companies always meet the latest requirements.
One of the essential logistics lessons learned is that compliance should not be an afterthought but an integral part of supply chain strategy. By investing in adequate technology, companies can automate compliance processes, reduce manual errors, and ensure they are always prepared to meet regulatory demands.
At Last Mile Logistics, we have the experience to adapt and tailor your transportation solutions to meet recent challenges. As we move forward, these supply chain management lessons will continue to be crucial in building resilient and adaptable supply chains. You can embrace this knowledge to be better equipped to handle future disruptions, turning challenges into opportunities for growth and success. So please call Arnie so we can evaluate your transportation needs.