September 23, 2024
Building Successful Construction Logistics Strategies
Efficiently managing the flow and storage of construction materials, from their origin to their final use, is known as construction logistics. This process is the backbone of any successful construction project, requiring comprehensive planning, meticulous implementation, and rigorous control. With a sufficient system in place, projects can avoid cost overruns, missed deadlines, and avoidable delays.
Let’s discuss the key elements of a robust construction logistics plan and how partnering with a trusted third-party logistics (3PL) provider can positively impact logistics efficiency and cost-effectiveness for construction businesses.
How Good Construction Logistics Reflects on Project Success
The industry constantly demands a fast-paced workflow, guaranteeing that supply chain operations run smoothly. Construction site logistics involves coordinating deliveries and pickups in compliance with safety regulations. At the core of this coordination is the construction logistics plan, which must be customized for each project to ensure the timely and accurate transportation of materials between construction sites, warehouses, and shipping facilities.
A proper logistics plan for construction projects considers several factors, including supply chain management, workforce scheduling, traffic planning, local regulations, and material storage. These logistical challenges must be addressed before construction begins to avoid disruptions that could derail a project.
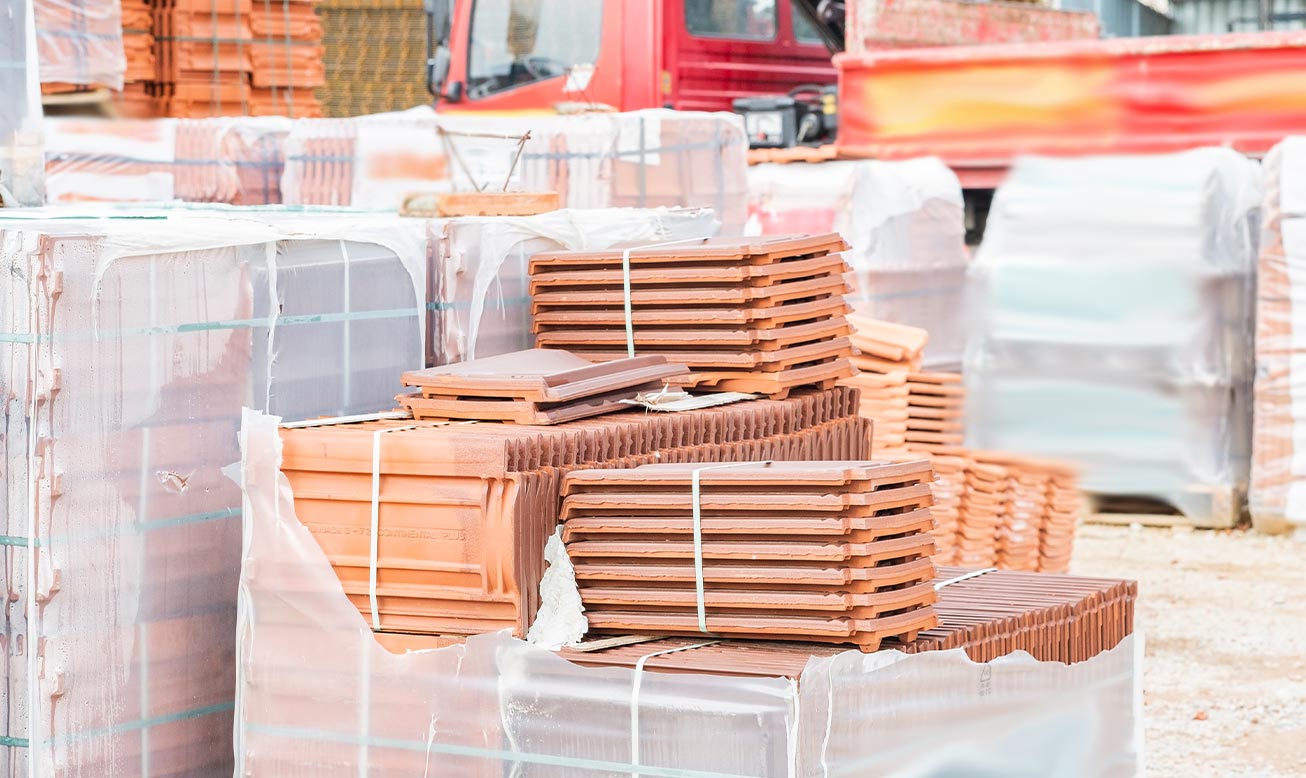
Logistics Planning and Scheduling as Foundations for Success
Every aspect of the project—from material procurement to transportation logistics—must be meticulously planned. Adequate planning reduces the risk of costly delays and ensures that construction teams have everything they need when they need it.
Integral elements of a comprehensive construction logistics plan include:
Material and transportation logistics – Coordinating material transportation to and from the construction site is integral to the project’s success. This approach requires sufficient route planning, managing transportation fleets, and ensuring deliveries comply with safety regulations.
Supply and demand – Balancing supply with the project’s demand is crucial to avoid material shortages that could delay construction or excess inventory, resulting in wastage.
Local access and infrastructure – Understanding site accessibility, traffic patterns, and infrastructure constraints helps ensure that materials and workers can move smoothly to and from the site.
Procurement planning – Establishing relationships with reliable suppliers and managing the timing of deliveries minimizes disruptions.
Addressing these factors well in advance allows construction companies to complete the project lifecycle and avoid unexpected hurdles confidently.
Site-to-Site Logistics: Challenges and Solutions
Construction projects often involve multiple sites that require a well-coordinated logistics network to facilitate the movement of materials, workers, and equipment. Construction site logistics can be particularly challenging without a robust transportation management system (TMS) that integrates with the company’s leading office software.
To ensure smooth logistics operations across sites, construction companies should:
Plan and coordinate routes to optimize transportation management
Oversee workforce schedules to ensure that the right personnel are on-site at the right time
Set up material storage areas that are easily accessible yet secure
Adapt to evolving project needs to keep logistics operations flexible
One of the most practical ways to manage these logistical challenges is to appoint a construction logistics manager. This professional is crucial in coordinating logistics activities and ensuring the seamless flow of materials and equipment.
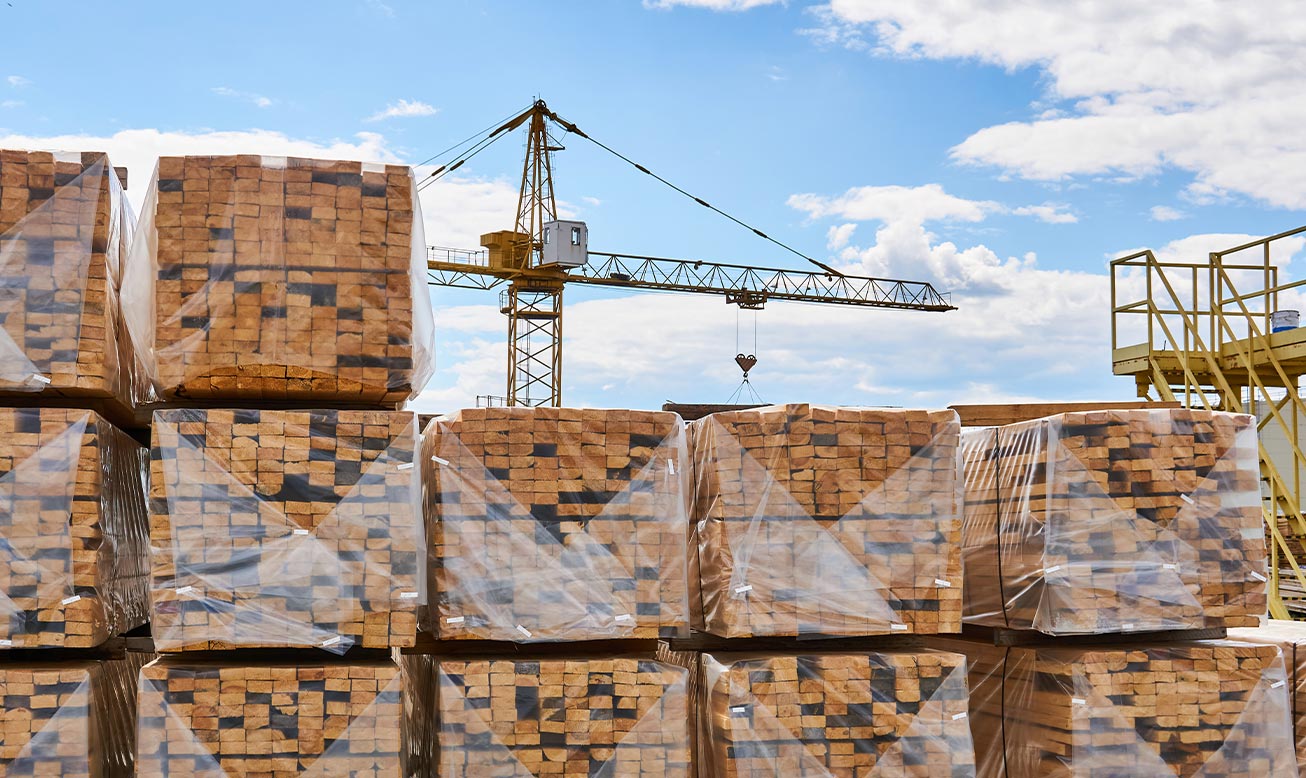
The Role of a Construction Logistics Manager
A construction logistics manager is responsible for overseeing the entire supply chain at a construction site, ensuring that materials, goods, and equipment are delivered on time and in the correct quantities. This role involves close collaboration with project planners, commercial managers, and construction site managers.
The primary duties of a construction logistics manager include:
Planning and scheduling – Creating detailed timelines for material deliveries and coordinating logistics with suppliers.
Supply chain management – Ensuring that materials are sourced from reliable suppliers and that the supply chain remains uninterrupted.
Safety and communication – Managing communication between various teams to maintain compliance with safety standards.
Delivery management – Overseeing deliveries to ensure they arrive on time and are correctly stored at the construction site.
Partnering with a 3PL Might Be the Key to Cost-Efficient Construction Logistics
Managing a complex supply chain in-house can be overwhelming for many construction companies. Partnering with a trusted third-party logistics provider (3PL) can offer significant benefits. A 3PL specializing in construction logistics solutions can streamline transportation, warehousing, and inventory management, freeing construction professionals to focus on its essential competencies.
A 3PL can provide the following advantages:
- 1
Expertise – 3PLs bring extensive industry knowledge in logistics planning and scheduling, helping construction companies develop tailored logistics plans.
- 2
Technology – Many 3PLs offer advanced logistics software that integrates with the company’s systems, providing real-time visibility into material movement and delivery schedules.
- 3
Cost savings – By optimizing transportation routes and reducing material handling inefficiencies, a 3PL can significantly reduce logistics costs.
- 4
Flexibility – 3PLs have the capacity to scale their operations based on the size of the construction project, ensuring that logistics solutions are always aligned with project needs.
Boosting Productivity with a Non-Asset-Based Carrier
A non-asset-based carrier operates without owning the trucks, warehouses, or shipping facilities used to transport goods. Instead, they use an extensive network of third-party providers to move materials, allowing them to offer greater flexibility and often more competitive pricing.
By partnering with a non-asset-based carrier, construction companies can:
Improve cost-effectiveness – Since non-asset-based carriers don’t have the overhead costs of owning assets, they can offer lower rates for logistics services.
Access a broader network – Non-asset-based carriers have partnerships with multiple providers, enabling them to discover optimal routes and cost-effective shipping choices.
Scale services quickly – As construction projects grow or shrink, non-asset-based carriers can easily adjust their services to meet changing logistics needs.
At Last Mile Logistics, we provide comprehensive building construction logistics solutions to help companies with their material transportation challenges. As a non-asset-based carrier, we can offer flexible, cost-efficient logistics services that ensure timely materials delivery.
Effective logistics in construction is critical to the success of any building project. Construction companies can significantly improve their logistics operations and reduce costs by developing a detailed construction logistics plan, appointing a logistics manager, and learning from our expertise.
Partnering with Last Mile Logistics will allow your construction firms to focus on what you do best: delivering high-quality construction projects on time and within budget. If you are ready to take your construction logistics to the next level, contact Arnie today to discuss your transportation needs.