February 18, 2025
KPIs for Evaluating Supply Chain Performance
As an owner, managing your business’ supply chain at maximum efficiency is one of the most critical factors for the success of your operations. A well-oiled supply chain keeps your business running smoothly, reduces costs, and keeps customers happy. But how do you know if your supply chain is performing at its best? The answer lies in the proper tracking of key performance indicators (KPIs). These metrics provide valuable insights into how your business is doing and where improvements can be made.
Let’s break down the most important metrics used to measure supply chain performance, from inventory management to warehouse operations. Whether you are new to supply chain management or looking to optimize your current processes, these KPIs for inventory, transportation, and warehouse efficiency will help you stay ahead of the game.
Why Rely on Supply Chain KPIs?
Think of supply chain KPIs as a report card for your business that tells you how well your supply chain is performing, highlights areas of improvement, and helps you make data-driven decisions. Without these metrics, you are essentially flying blind, which can result in higher costs, inefficiencies, and unhappy customers.
Focusing only on chain efficiency can improve customer satisfaction, reduce waste, and streamline operations. However, to do that, you need to know which metrics to evaluate supply chain performance are most relevant to your business. Here are some of the most critical ones.
1. Order Rate: The Foundation of Supply Chain Efficiency
The order rate is one of the most commonly used KPIs for inventory management and overall supply chain performance. It measures your ability to fulfill orders accurately and on time. A high order rate means your supply chain is running smoothly, while a low rate could indicate issues like delays, errors, or stockouts.
To achieve an effective order rate, your business should meet the following criteria:
The shipment leaves the warehouse on time.
The order is received correctly (no damaged or missing items).
The shipment contains the right quantity of items.
No returns due to errors or defects.
No payment issues or disputes.
Tracking your order rate helps you identify bottlenecks in your supply chain, such as shipping delays or inventory management errors. By promptly addressing these issues, you can boost your bottom line and improve customer satisfaction.
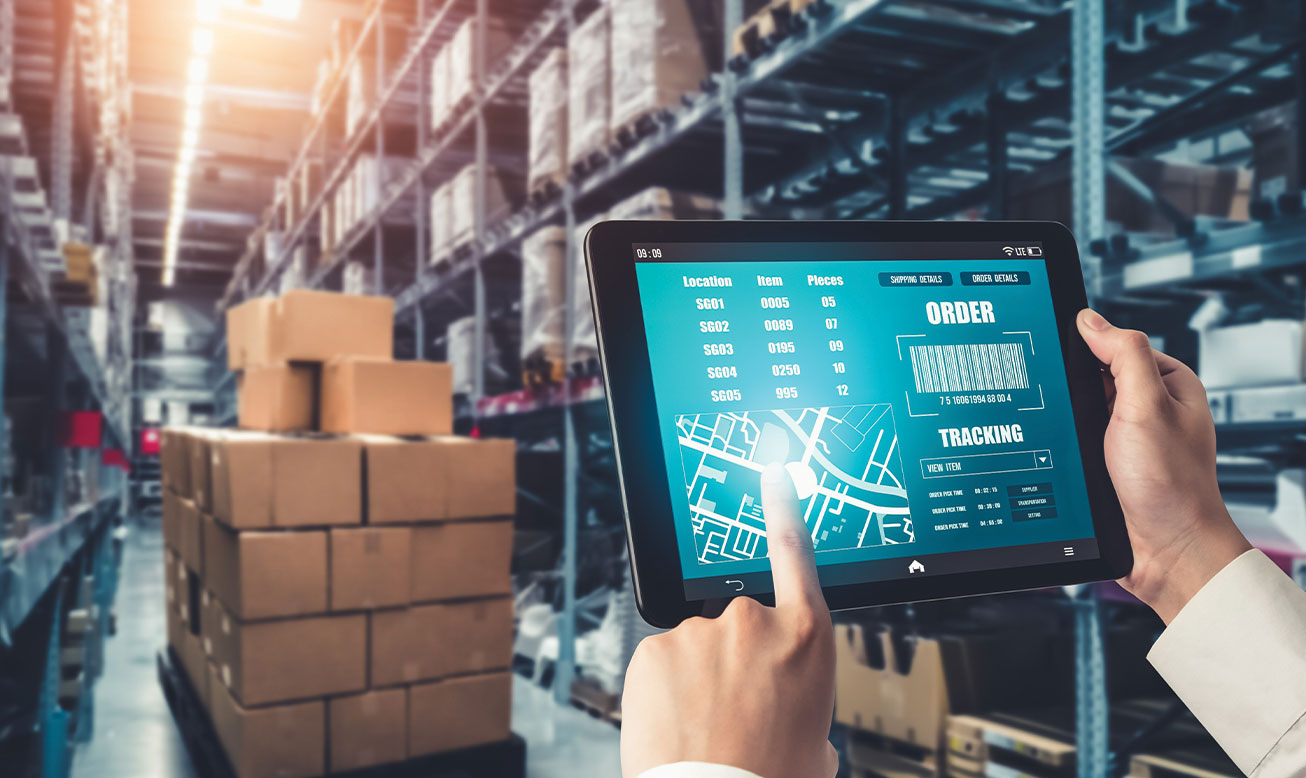
2. Supply Chain Cycle Time: Speed Matters
Another critical supply chain KPI is supply chain cycle time. This metric measures how long it takes to fulfill an order from when it is placed to when it’s delivered. A shorter cycle time means your supply chain is agile, flexible, and resilient, qualities that are essential in today’s fast-changing market.
To calculate your supply chain cycle time, you need to track the following steps:
When orders are received.
When orders are processed and ready to be delivered.
Date and time of shipping.
Date and time of receiving.
By analyzing this data, you can identify areas where delays occur and take steps to streamline your processes. For example, if your cycle time is longer than industry standards, you might need to optimize your inventory management or improve coordination with your logistics partners.
3. Inventory Turnover: A Key KPI for Inventory Management
Inventory turnover, also known as inventory velocity, is a crucial warehouse KPI that measures how many times your entire inventory is sold and replaced over a specific period. A high turnover rate indicates healthy sales and efficient inventory management, while a low rate could mean you are overstocked or struggling to sell your products.
To calculate inventory turnover, you need the following data:
Cost of items sold.
Average inventory.
The ratio of how many times a stock is sold and replaced over a set period.
Comparing your inventory turnover rate with industry benchmarks or direct competitors can provide valuable insights into your supply chain’s performance. If your turnover rate is lower than average, it might be time to reevaluate your inventory management strategies.
4. Demand Satisfaction Rate: Keeping Customers Happy
The demand satisfaction rate is an essential supply chain KPI that measures how well you are meeting customer demand. Specifically, it tracks the percentage of orders fulfilled by stock availability without lost sales or backorders. A high demand satisfaction rate means you are keeping customers happy and minimizing missed opportunities.
To calculate this metric, you need to track:
Order date.
Delivery time.
The number of orders met on time.
Total number of orders received.
Improving your demand satisfaction rate often involves optimizing your inventory management and forecasting processes. Ensuring you have the proper products in stock at the right time might reduce lost sales and improve customer loyalty.
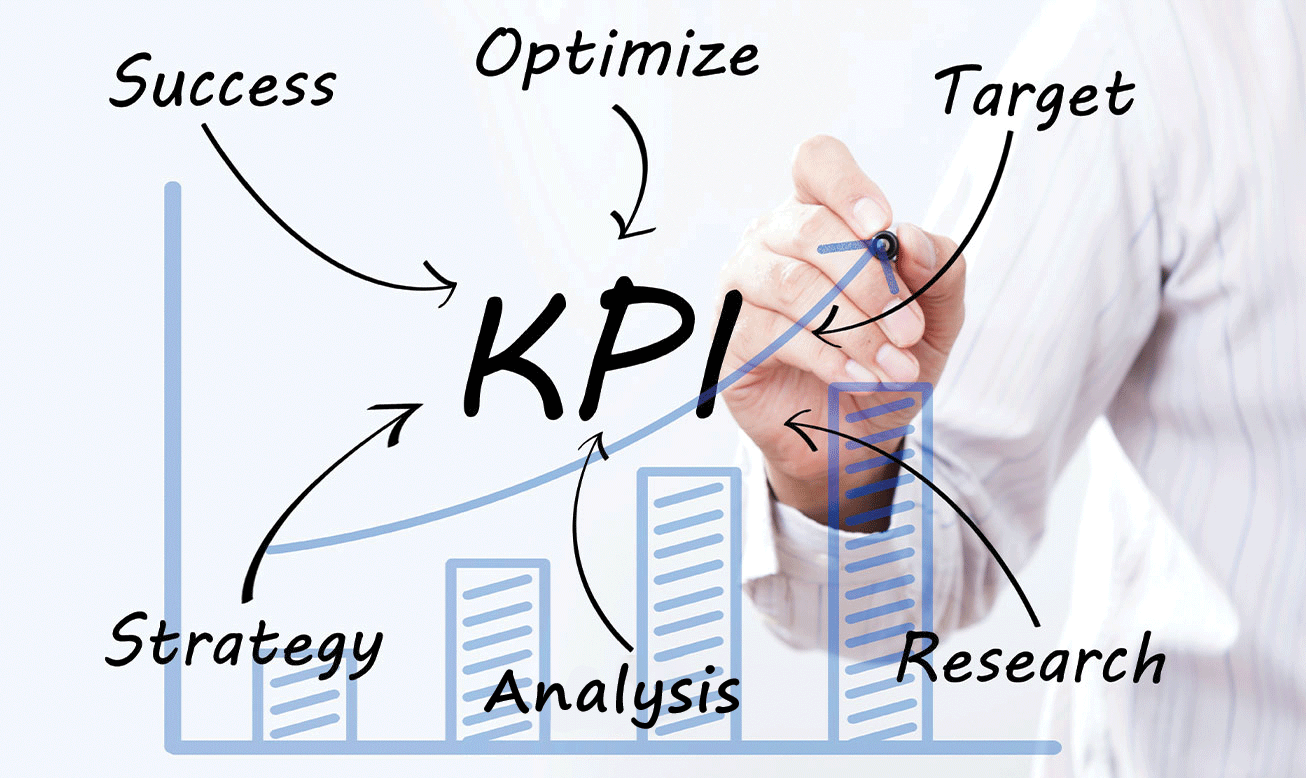
5. Warehouse Metrics: The Backbone of Supply Chain Efficiency
Your warehouse is the heart of your supply chain, and tracking warehouse metrics is essential for maintaining supply chain efficiency. Some of the most important warehouse KPIs include:
Order picking accuracy – Measures how often orders are picked correctly.
Inventory accuracy – Tracks the accuracy of your inventory records.
Warehouse capacity utilization – Measures how effectively you’re using your warehouse space.
Shipping accuracy – Tracks the percentage of orders shipped without errors.
By monitoring these metrics, you can identify inefficiencies in your warehouse operations and take steps to improve them. For example, if your order picking accuracy is low, you might need to invest in better training or technology.
How to Improve Your Supply Chain KPIs
Now that you know which metrics to evaluate supply chain performance, the next step is to take action. Here are a few tips to help you improve your supply chain efficiency:
Invest in technology – Tools like inventory management software and transportation management systems can help you track KPIs in real-time and make data-driven decisions.
Optimize inventory management – Regularly review your inventory levels and adjust them based on demand forecasts.
Streamline processes – Identify bottlenecks in your supply chain and take steps to eliminate them.
Collaborate with partners – Work closely with your suppliers and logistics providers to ensure smooth operations.
Tracking supply chain KPIs is paramount for any business striving to stay competitive. By focusing on metrics like order rate, supply chain cycle time, inventory turnover, and demand satisfaction rate, you can identify areas for improvement and take steps to optimize your operations.
But remember, supply chain efficiency is not a one-time effort but an ongoing process. Regularly monitoring your warehouse metrics and other KPIs will help you stay competitive and keep your customers happy.
If you are looking for expert guidance on improving your supply chain, consider partnering with a trustworthy logistics provider like Last Mile Logistics; with years of experience and a commitment to tailored solutions, we can help you with your transportation goals and take your supply chain to the next level.
So, what are you waiting for? Start tracking these metrics to evaluate supply chain performance today and watch your business thrive!